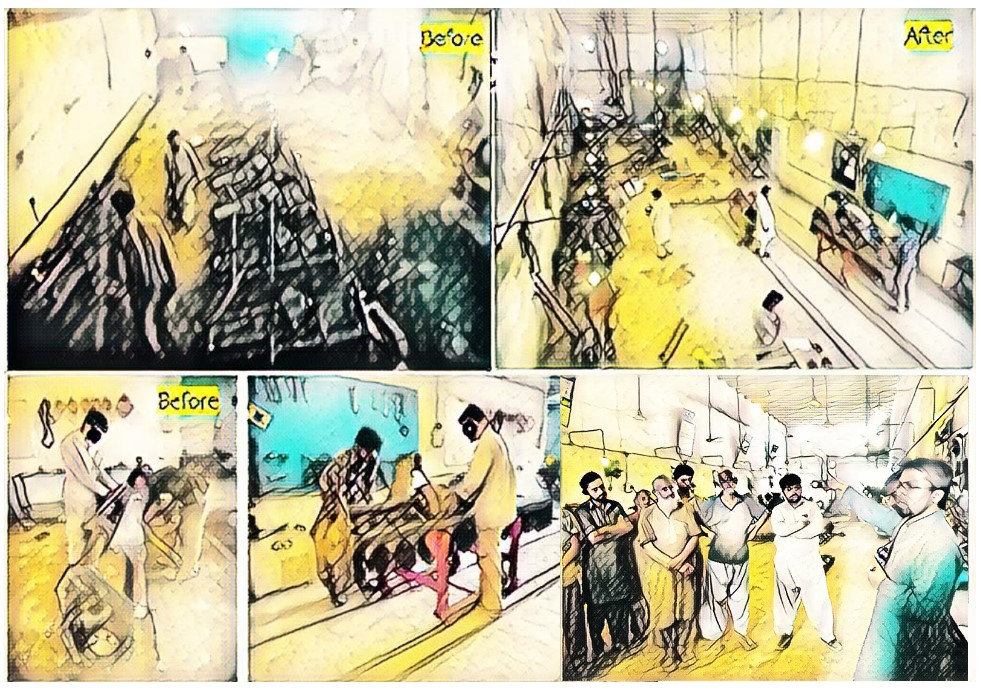
During 2013-2014, as part of a special project for a foreign customer, I spearheaded an effort to streamline the assembly process of agricultural implements through the introduction of a new trolley system. With the active cooperation of the production team and leadership commitment, we were able to decrease lead time from 7.5 hours to 4.19 hours, dramatically enhancing efficiency, productivity, and ergonomics for workers.
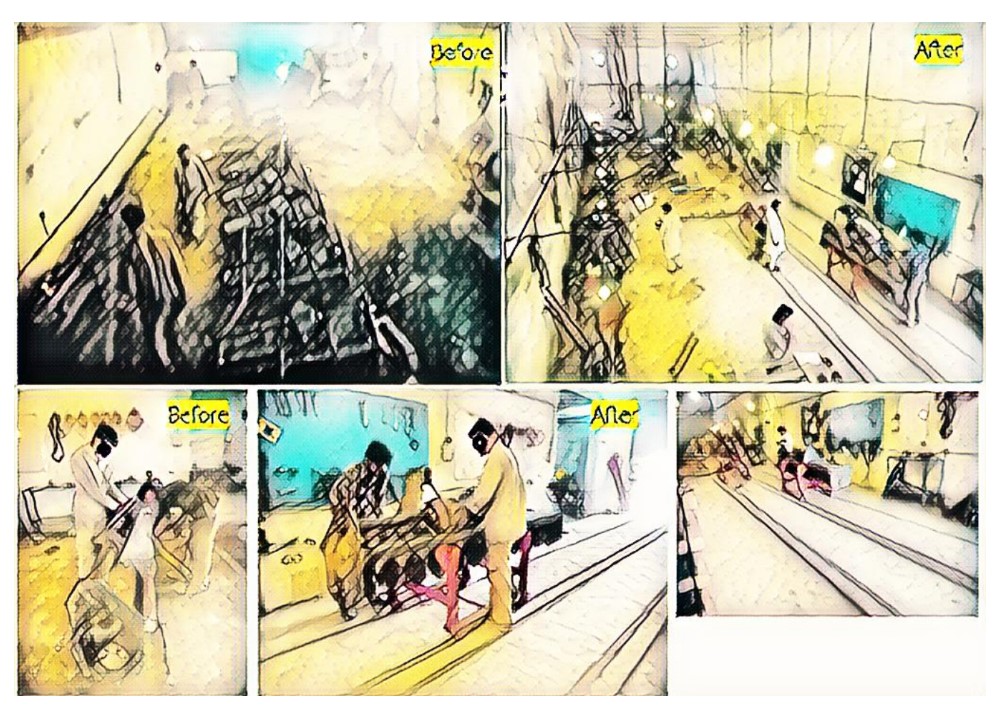
The Challenge: Prior to the intervention, the assembly process was plagued by a series of inefficiencies:
- Long lead times due to unnecessary movement by workers and ineffective material handling.
- High incidences of non-value-adding activities, including tool and component searching.
- Ergonomic issues, resulting in worker fatigue and uneven production rate.
- Lack of standardized material flow, resulting in frequent congestion and bottlenecks in production.
The Approach: Utilizing my skills in continuous improvement, industrial engineering, and lean principles, I developed a systematic improvement plan to:
- Process Mapping & Waste Identification Executed a value stream mapping (VSM) exercise to identify critical bottlenecks in the assembly process. Applied root cause analysis (RCA) to study inefficiencies in material handling and movement.
- Experimental Development of the Trolley System To eliminate inefficiencies, we went through several design iterations before arriving at the optimal trolley system:
Prototype 1: A basic stationary workstation to position tools and materials within reach, but it failed to remove unnecessary movement.
Prototype 2: A fixed-frame trolley with shelves, which enhanced accessibility but was cumbersome to move around the shop floor.
Prototype 3: A wheeled trolley system, providing mobility but without stability on uneven floors.
Final Design: A fully mobile, balanced trolley, with:
- Optimized weight distribution for stability.
- Durable wheels for smooth movement across different floor conditions.
- Dedicated slots for tools and components, making them easily accessible.
3. Work-in-Progress (WIP) Flow Optimization Implemented a kanban-based pull system to synchronize trolley usage with production requirements. Streamlined shop floor layout to facilitate free trolley and material flow.
4. Workforce Engagement & Leadership Support Scheduled training sessions to standardize assembly operations with the new trolley system.
Fostered continuous feedback from production staff, resulting in further trolley design enhancements.
Strong leadership commitment ensured resource allocation, accelerating implementation and promoting a culture of continuous improvement.
The Results
The combined effort of the production team, management, and leadership yielded astounding improvements:
- Lead time decreased from 7.5 hours to 4.19 hours (44% decrease).
- Worker productivity improved, thanks to the minimized need for unnecessary movement.
- Worker fatigue was significantly reduced, enhancing engagement and efficiency.
- Enhanced consistency in assembly quality, as all the required materials were organized systematically.
- The trolley system was utilized as a model for future process enhancements.
Key Takeaways & Lessons Learned
Collaboration is the key: This transformation was possible only because of the production team’s commitment and leadership’s commitment to continuous improvement.
Experimentation drives innovation: Each prototype enhanced the final trolley design, demonstrating that incremental improvements yield breakthrough results.
Material flow optimization yields massive gains: An optimized trolley system eliminated waste, minimized delays, and boosted productivity.
Leadership support accelerates change: When leadership actively supports process improvement initiatives, implementation is faster and more effective.
Conclusion:
By applying lean principles, experimentation, and leadership support, we effectively transformed the agriculture implement assembly process, resulting in faster production, enhanced quality, and enhanced worker efficiency. This case study demonstrates that genuine operational excellence is attained through teamwork, innovation, and leadership commitment. improvement professionals!